APPLICATION
Equipment package for the production of radiators for heating systems. Product parameters and equipment performance are agreed in the terms of reference.
Typical specifications of radiators:
- Power: 360-9.000W
- Product size: 300, 400, 500, 600, 900mm
- Radiator length: 400-3,000mm
- Types: 10,11.20,21, 22 (standard), 33
FEATURES
The equipment is automated and integrated into a single production chain – a radiator manufacturing plant.
The plant consists of the lines for:
- Punching
- Welding
- Powder painting
- Packaging
The lines contain all the necessary equipment for the production of 360-650 thousand units per year. Three-shift operation is planned. Radiator assembly and some technological operations are performed manually.
Additional equipment is used to increase the automation of assembly and packaging, as well as for increasing the line performance and applying highly durable paint.
PRODUCT LINE
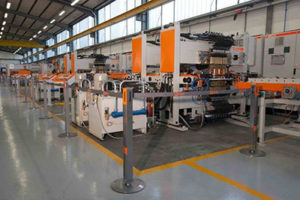
Manufacturing of the halves of the radiator cases, grilles, and brackets. The machines are automated and operated by a controller. The operating modes are set by the operator.
The line starts with the steel feed system. It consists of a hydraulically driven uncoiler and a device that feeds the steel sheet to the machine.
The equipment is characterized by high accuracy of sheet feeding (±0.01 mm). The controller synchronizes the operation of the coil openers and pushers, as well as straightening and feeding devices.
A high-precision forming and cutting press is used for the production of case halves. The press machine operation modes and speed are controlled from the control panel with the controller. The control unit is equipped with the necessary switches and indicators.
The punching press is equipped with a tool with programmable dies. Various tooling is used to produce panel halves for the production of undulate radiators, grilles, end faces, and brackets.
The hydraulic system of the press is protected with a device that reduces the pressure in the cylinder in case of overload. The device protects the press from locking in the lower position when setting the die.
Line capacity:
- 240m/h (700-900mm radiators)
- 480 m/h (300-600mm radiators)
The line is equipped with an automatic lubrication system. A compact roller conveyor moves workpieces from the press machine to the welding line
Specification
- Panel material: cold-rolled steel DC-01 (1.1-1.2mm)
- Convector material: St12 steel (0.35-0.5mm)
- Feeding unit capacity (t): 10
- Maximum roll width (mm): 1,000
- Steel thickness (mm): 0.4-1.5
- Number of programs: 127
- Length (mm): 0.05- 9999.99
- Feed mechanism accuracy (mm): 0.05-9.9
- Function selection: single stroke/automatic
- Quick-change press die
- Modem for teleservice
- Counter of units and strokes
- Diagnostics
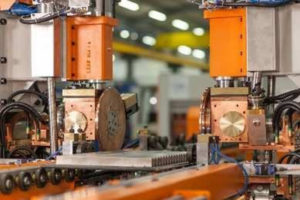
Линия сварки состоит из оборудования для двухрядной и продольной сварки панелей радиаторов.
Скорость и параметры сварки контролируются электроникой. Контроллеры имеют Ethernet интерфейс для управления через панель оператора и ПК.
Панели радиатора перемещаются по линии сварки с помощью сервоприводов.
Основные технологические узлы и операции сварочной линии:
Блок 1
- Подача половин корпусов на входной рольганг
- Центрирование половин корпусов и монтаж опорных колец
- Поворот
Блок 2
- Предварительное скрепление половин панелей
- Двухрядная многоточечная сварка
- Ручная загрузка конвекторов
- Центрирование и позиционирование конвекторов
- Двухрядная многоточечная сварка
Блок 3
- Двойная продольная сварка модулей панелей
- Продольная обрезки кромки (фрезерный станок)
- Двойная поперечная сварка модулей панелей
- Нарезка на панели
Блок 4
- Обрезка кромки и пробивка отверстий
Блок 5
- Поворот панелей на 180⁰
- Монтаж радиаторов и приварка кронштейнов
Блок 6
- Испытания на стенде (1-3 радиатора)
Dimensions of workpieces
Radiator length (mm) | Quantity | Workpiece length (mm) |
400 | 4 panels | 1,600 |
500 | 4 panels | 2,000 |
600 | 4 panels | 2,400 |
700 | 4 panels | 2 800 |
800 – 1 000 | 3 panels | 2 400 – 3 000 |
1 100 – 1 500 | 2 panels | 2 200 – 3 000 |
1 600 – 3 000 | 1 panel | 1 600 – 3 000 |
The minimum workpiece length is 1,600 mm (4x400mm, 1×1,600mm)
Number of welding points
Radiator height (mm) | Panel | Convector (without cutouts) |
300 | 7 (with a shunt) | 7 (with a shunt) |
400 | 10 | 10 |
500 | 13 (with a shunt) | 13 (with a shunt) |
600 | 16 | 16 |
700 | 18 | 18 |
900 | 24 | 24 |
The powder coating line consists of a chamber, a double conveyor, a pre-treatment and drying section. The coating paint line speed (2.5m/min) is coordinated with the welding section speed.
Radiator workpieces are pre-treated by immersing in a tank with a primer. Radiators are dried in a gas-heated chamber.
The polymerization chamber is made of stainless steel. It has an axial cylinder and 6 automatic nozzles. There are a cyclone and filters for cleaning the gas medium. The curing oven is heated by gas.
The chamber conveyor has C-shaped hooks that ensure uniform coloring of products.
Main process steps on the line are:
- Pre-treatment (priming)
- Pre-drying
- Immersion in an adhesion enhancer
- Drying
- Cooling
- Automatic powder coating (epoxy-polyester, 60-100pm, sintering at 190°C)
- Polymerization chamber
- Cooling and unloading
- Maximum product length (mm): 3,000
- Maximum product width (mm): 300
- Maximum product height (mm): 900
- Maximum weight (kg): 200 – on 2 hooks
- Average load (kg/m): 80
- Average speed (m/min): 2×2.5
- Paint drying time at 80-150°C (min): 17
- Powder curing time 190-230°C (min): 28
Packing of finished products in a protective film is partially automated and consists of the following process steps:
- Semi-automatic unloading of radiators from the coating line conveyor.
- Manual installation of the upper grid and side cover on the conveyor
- Packing of the radiator in a box (manual)
- Installation of protective edges (manual)
- Wrapping in film and cutting the film (automatic)
- Unloading of packaged radiators (manual)
OPTIONS
- Magnetic gripper is a device for automatic loading of half cases on the welding line conveyor. It helps to reduce downtime and process interruptions
- Plug installation device for installing the plastic plugs on all radiator connections.
- Automatic suspension system on the coating line conveyor is a transport system before of the coating line that regulates the speed and height of hanging radiators. The operator hangs the hooks on a chain and inserts them into the holes in radiators
- Electrophoretic coating equipment consists of a chamber and related equipment for coating radiators with a scratch and corrosion resistant paint (the technology is used for painting cars)
SELECTION
To select a line with the suitable capacity and products size, please, leave a request to our specialist