APPLICATION
Tubular electric heating elements (TEN) are used as heaters for equipment for industrial and domestic use. Heating elements can heat water, oil, air, liquid, and gaseous heat carriers.
Tubular heaters are used in the manufacture of equipment:
- Heat guns
- Evaporators
- Raw materials melt blocks (PVC, ABS, etc.)
- Ovens
- Hot water boilers
- Press forms
- Water and oil baths
- Washing machines
- Hotplates
- Electric kettles
- Air heaters
- Distillers
Tubular heaters are characterized by a simple and flexible design. Using the heating element, you can obtain a heater of the desired shape with the required heat transfer area.
FEATURES
Advantages of tubular electric heating elements in comparison with other heaters:
-
- No stress on the shell
- Direct contact with the heated environment is allowed
- Withstand vibration and shock
- Heaters of complex geometry can be manufactured
- Powerful heating blocks can be assembled
The use of tubular electric heating elements is limited by the chemical resistance of the housing material to the media and the temperature that its elements can withstand. Tubular electric heating elements can not be used in explosive environments
Finned heaters
To heat the air, there are versions with an increased surface area – finned heating elements. The fins are made of corrugated steel or aluminum strip tightly wound on the heater body. The surface area of a finned fuel cell is 2-2.5 times larger than of a regular cell.
Cartridge heaters
Cartridge tubular heaters are convenient for applications that require the placement of contacts on one side of the heater. They are used for heating injection molds and containers.
Specification
• Power: 0.63-15kW
• Operating voltage: 36-380V
• Diameter: 8, 10, 12, 13 and 16mm
• Length: 20-320cm
• Sheath: carbon and stainless steel, heat-resistant seamless steel 12X18H10T
• Diameter of the fitting/lobe: M14, M16, M18, M20, M22, and M24x1.5. Standard ― G1/2‘
• Fitting: steel, stainless steel, brass
• Dielectric: periclase
• Bending radius: >1.5 diameter of the heater
STRUCTURE AND OPERATION
Heat is transferred from a tubular electric heater by convection, heat conduction, and radiation.
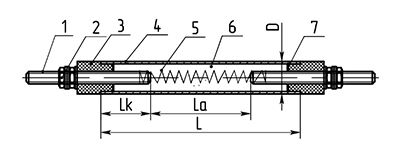
The tubular electric heater includes an electrically conductive thread (5) with high resistance, which is placed inside a metal sheath (4). The thread is separated from the body with a heat-conducting dielectric layer (6). The contact rods (1,2) are isolated from the fuel cell housing in contact with the medium by a dielectric material (3). The connections are sealed (7).
The thread is made of a heat-resistant alloy – nichrome/fechral. Its thickness and the winding degree determine the specific heat output of the heater.
The tubular electric heater body is made of acid-resistant stainless steel (SS304). It can briefly withstand temperatures up to 900 ⁰C.
PRODUCT LINE
Grade | Power density (W/cm2) | Medium | Body material | Application area |
Х | 11 | Water, weak solution
of alkali/acid (pH 5-9) |
Copper and brass (coated) | Heating from T<100 ⁰C |
Р | 11 | Water, weak solution
of alkali (pH 7-9) |
Stainless steel | |
П | 11 | Water, weak solution
of alkali/acid (pH 5-9) |
Carbon steel | |
С | 2.2 | Air | Carbon steel | Heating of a still medium T<500⁰C |
T | 5.2 | Air | Stainless steel | Heating of a still medium T<700⁰C |
О | 5.5 | Air | Carbon steel | Heating of a moving medium >6 m/s T<500⁰C |
Э | 2.5 | Air | Carbon steel | Heating of a moving medium >6 m/s T<500⁰C |
И | 3 | Fats and oils | Carbon steel | Heating in baths T<300⁰C |
У-1 | 18 | Soles of electric irons | Carbon steel | Poured into a metal platform, T<500 °C. |
У-2 | 13 | Soles of electric irons, aluminum alloy plates, steel, and cast iron forms | Carbon steel | Inserted into the groove and pressed, T<500 °C. |
· Grade | Power density (W/cm2) | Medium | Body material | Application area |
X | 9 | Water, weak solution
of alkali/acid (pH 5-9) |
Coated copper/brass | Heating from T<100 ⁰C |
J | 15 | Water, weak solution
of alkali/acid (pH 5-7) |
Stainless steel | |
P | 15 | Water, weak solution
of alkali/acid (pH 7-9) |
Carbon steel | |
S | 2.2 | Air, gas mixtures | Carbon steel | Heating of a still medium Т<450⁰С |
T | 5 | Air, gas mixtures | Stainless steel | Heating of a still medium Т>450⁰С |
O | 5.5 | Air, gas mixtures | Carbon steel | Heating of a moving medium up to 6 m/s Tmax=450⁰C |
K | 6.5 | Air, gas mixtures | Stainless steel | Heating of a moving medium >6 m/s Т>450⁰С |
R | 3.5 | Air, gas mixtures | Carbon steel | Heating of the moving medium <6 m/s Тmax=450⁰С |
N | 5.1 | Air, gas mixtures | Stainless steel | Heating of the moving medium <6 m/s Т>450⁰С |
Z | 3.0 | Oils | Carbon steel | Heating of baths |
ZN | 3.0 | Oils | Stainless steel | Heating of baths |
V | 3.5 | Alkali, mixture
of alkali-nitrate |
Carbon steel | Heating and melting in baths Tmax=600⁰C |
W | 3.5 | Low-melting metals
(tin, lead) |
Carbon steel | Heating and melting in baths Tmax=450⁰C |
L | 5.0 | Molds | Carbon steel | Heating and melting of metal Tmax=450⁰C |
LN | 5.0 | Molds | Stainless steel | Heating and melting in baths Tmax=450⁰C |
Y | 13.0 | Aluminum plates | Carbon steel | Heating and melting in baths Tmax=320⁰C |
SELECTION
To select a suitable model of a tubular electric element, please, leave a request to our specialist. In the request, describe the task that you need to solve.